Procesowo i aparaturowo granulacja może być realizowana: bezciśnieniowo lub ciśnieniowo. Granulacja bezciśnieniowa może być prowadzona w złożu fluidalnym lub w swobodnie przesypującej się warstwie materiału granulowanego (granulatory dynamiczne, granulatory bębnowe, talerzowe, wibracyjne). Jeżeli granulacji podlegają surowce proszkowe, to niezależnie od tego, czy jest to granulacja ciśnieniowa, czy bezciśnieniowa, wykorzystuje się w procesie aglomeracji ciecz wiążącą.
Do najistotniejszych zalet granulacji bezciśnieniowej realizowanej głównie w granulatorach dynamicznych można zaliczyć:
- zmianę postaci materiałów drobnoziarnistych na zgranulowaną,,
- zmniejszenie emisji pyłów w czasie procesu technologicznego wpływające na obniżenie szkodliwych czynników pracy,
- poprawę osypliwości materiałów, co ułatwia ich dozowanie,
- zapobieganie segregacji w materiałach wieloskładnikowych,
- wyeliminowanie zbrylania się materiału,
- łatwiejszy transport i dozowanie zgranulowanych materiałów,
Granulację produktów stosuje się w wielu technologiach wytwórczych. Ze względu na wielkość produkcji dominuje przemysł chemiczny, ale równie często stosuje się granulację w przetwórstwie żywności, jak również w wielu technologiach związanych z inżynierią środowiska. W przemyśle chemicznym formowane granulki nawozów dają możliwość uzyskania specjalnych właściwości dotyczących szybkości ich rozpuszczania. Klasyczne metody granulacji bezciśnieniowej są też stosowane do wytwarzania granulek wieloskładnikowych w takiej postaci, że poszczególne składniki nakładane są w formie warstw powierzchniowych, co determinuje kolejne ich uwalnianie w wyniku rozpuszczania.
Granulacja, określana również jako aglomeracja, peletyzacja, grudkowanie jest procesem łączenia drobnych cząstek, takich jak pyły, proszki w większe agregaty (granule), o określonej wytrzymałości mechanicznej o wielkości granulek powyżej 1 mm. Sam proces aglomeracji lub granulacji odbywa się za pomocą granulacji na mokro z dodatkiem cieczy lub alternatywnie za pomocą granulacji na gorąco.
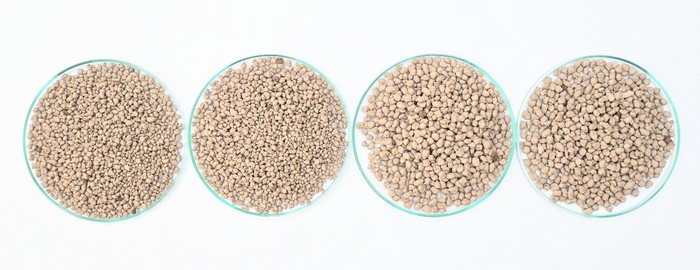
Granulat bentonitu
Mikrogranulacja to proces wytwarzania granulatów o wielkości granulek poniżej 1 mm. Ten rodzaj granulacji do niedawna był domeną suszarni rozpyłowych i granulatorów fluidalnych. Obie te technologie mają liczne wady. Proces granulacji w suszarni rozpyłowej wiąże się z bardzo wysokim zużyciem energii z tego względu, że materiałem wyjściowym do granulacji jest gęstwa o zawartości wody 40-50% i ta woda musi być odparowana w urządzeniu o bardzo niskiej sprawności cieplnej, natomiast granulki w dużej części są puste w środku. Granulat z granulatorów fluidalnych jest bardzo nieregularny i przypomina swoim kształtem jagody jeżyn.
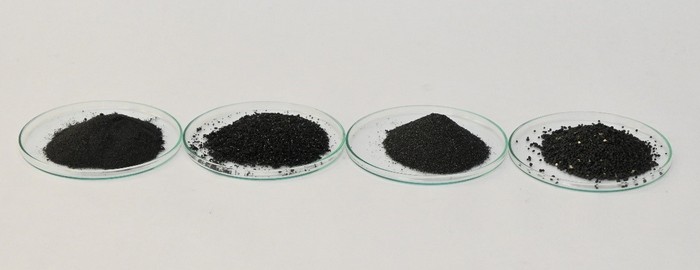
Mikrogranulat proszku odlewniczego do odlewania stali
Wytwarzanie mikrogranulek może być realizowane w granulatorach dynamicznych, gdzie duże szybkości przemieszczania materiału w obrębie wirnika (turbiny) umożliwiają uzyskiwanie również mikrogranulek. Stosowanie specjalnych wirników wspomaga ten proces i w warunkach przemysłowych uzyskiwanie granulatów w zakresie wielkości 0,1 do 0,7 mm jest osiągalne. Te zakresy uziarnienia granulek są np. pożądane w produkcji propantów i granulatów do formowania ciśnieniowego wyrobów ceramicznych, itd. Jednym z bardziej perspektywicznych obszarów zastosowania mikrogranulacji w granulatorze dynamicznym jest produkcja granulatu do wytwarzania płytek ceramicznych i ceramicznych wyrobów formowanych ciśnieniowo, w tym izostatycznie. Jest to rozwiązanie bardzo ekologiczne w porównaniu z aktualnie stosowaną technologią polegającą na przemiale surowców na mokro i granulacji gęstwy w suszarni rozpyłowej. Przedstawione techniki granulacji materiałów o specyficznych właściwościach jak również wykazane możliwości kształtowania nie tylko wielkości granulek, ale co równie istotne ich mikrostruktury jednoznacznie świadczą o wysokim stopniu uniwersalności intensywnego mieszalnika w procesach produkcji granulatów dla różnorodnych zastosowań. IdeaPro oferuje szeroki zakres urządzeń do granulacji mechanicznej, obejmujący dynamiczne mieszarki – granulatory typu MDV oraz MD oraz dyski aglomeracyjne. Oferowana technologia granulacji, dzięki zastosowaniu unikalnej sekwencji mieszania/granulacji, spełnia najwyższe standardy w zakresie jakości produktu, zużycia energii i wydajności z jednostki objętościowej urządzenia technologicznego. Połączenie w jednym urządzeniu fazy intensywnego mieszania i procesu granulacji doskonale sprawdza się w procesach granulacji wielu materiałów m in. nawozów wieloskładnikowych, pyłów itp.
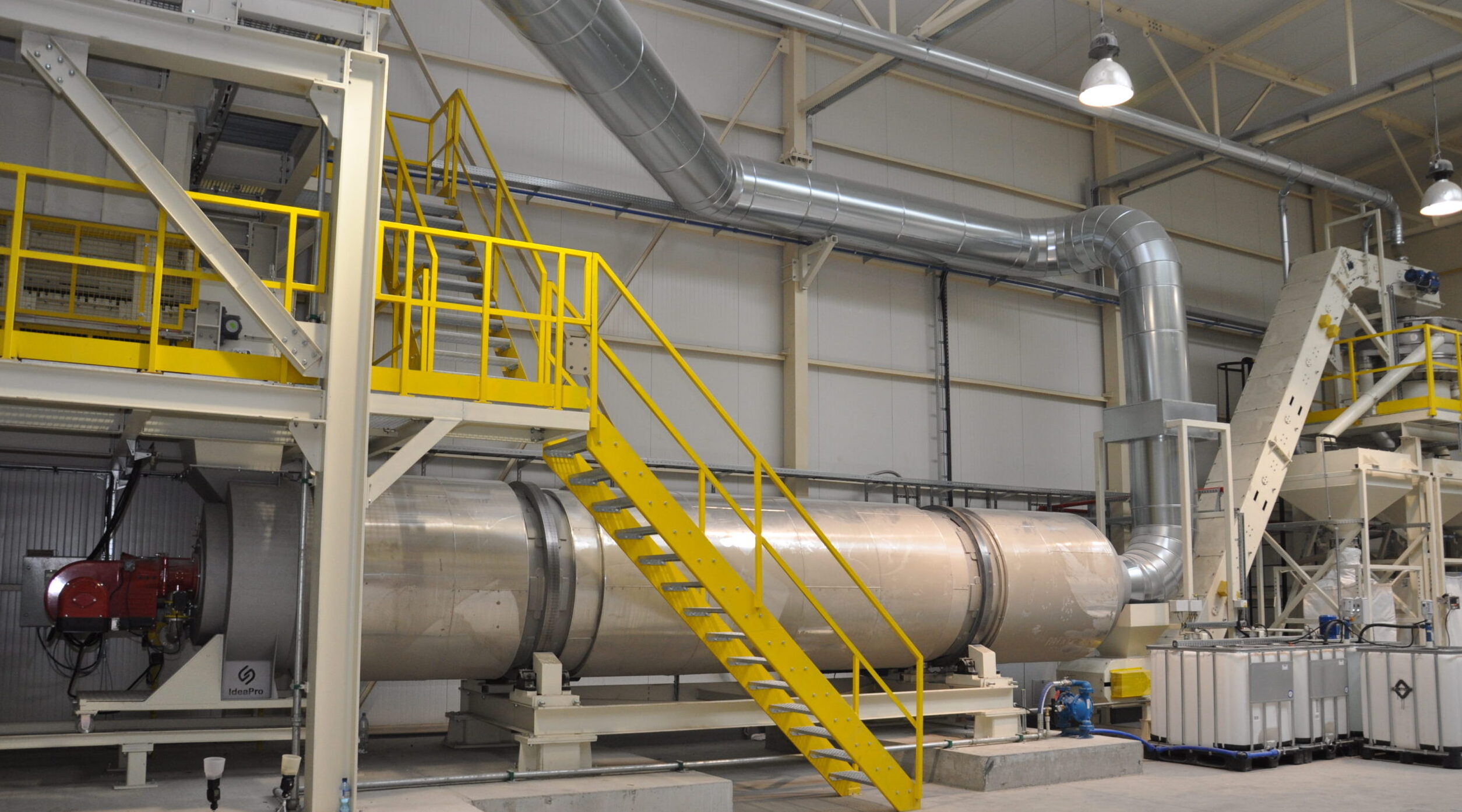
Linia granulacji, suszenia i przesiewania granulatów wapiennych
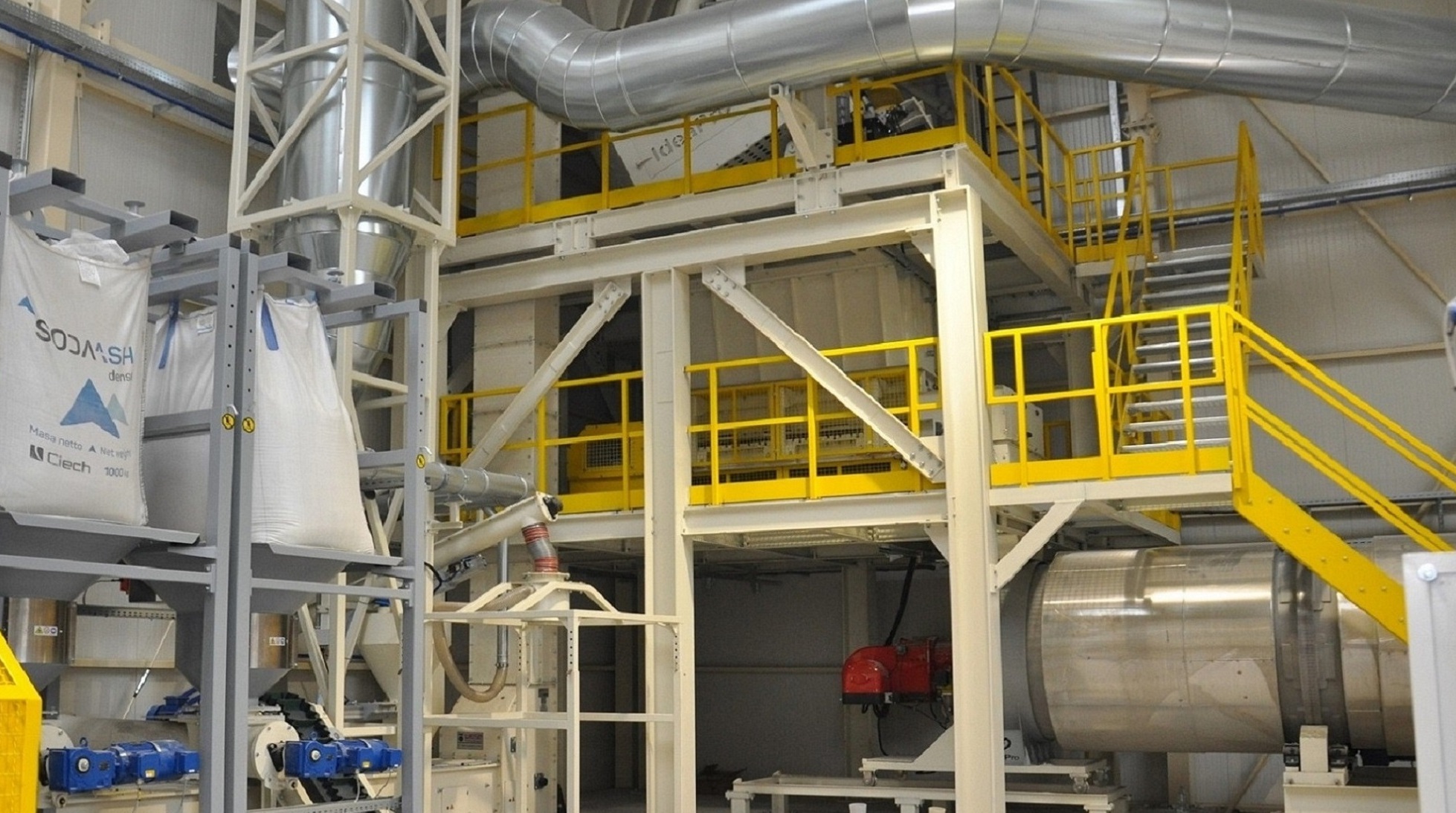
Linia granulacji i suszenia materiałów sypkich i proszkowych
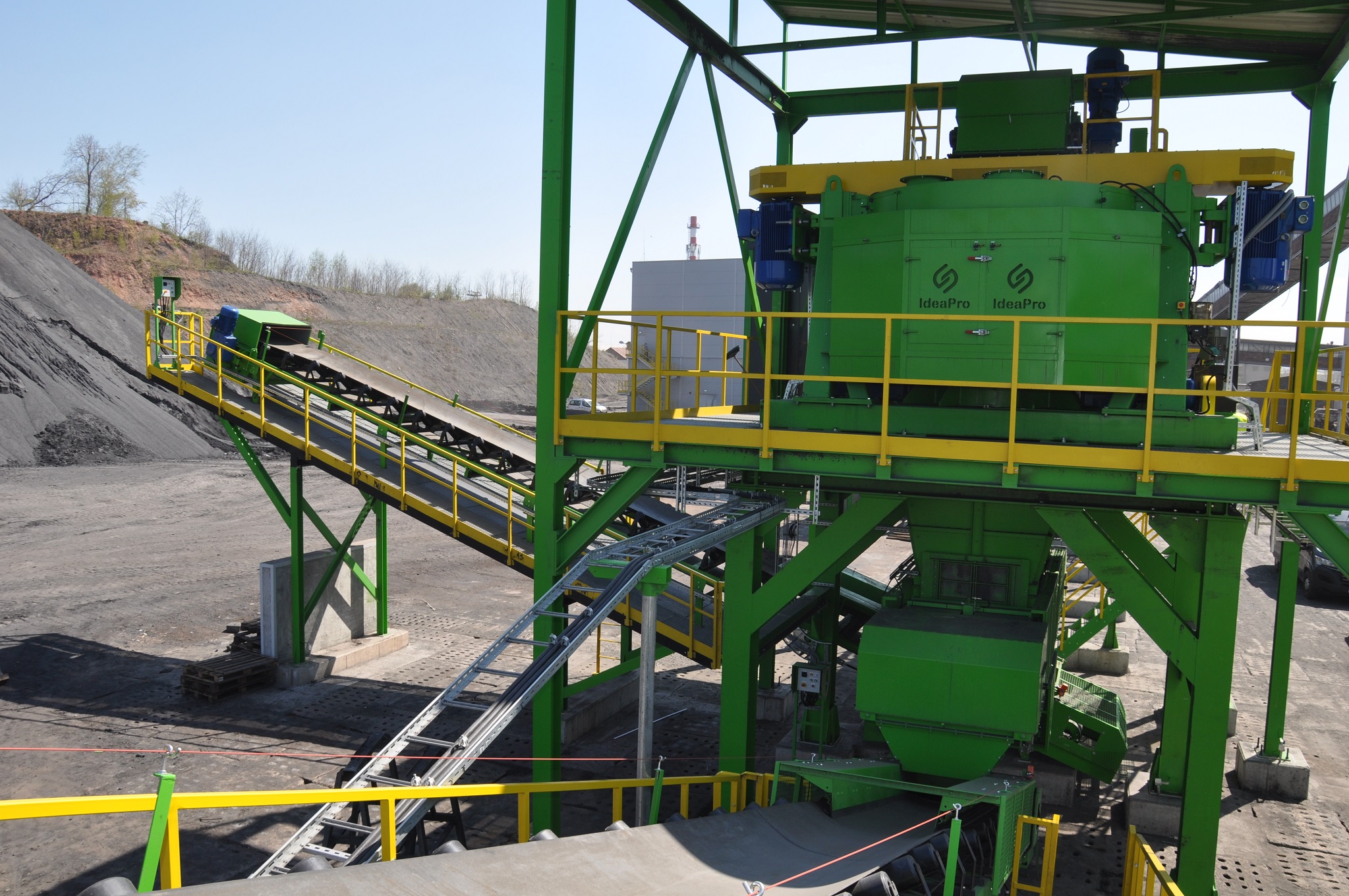
Linia granulacji miału węglowego z pyłem węglowym
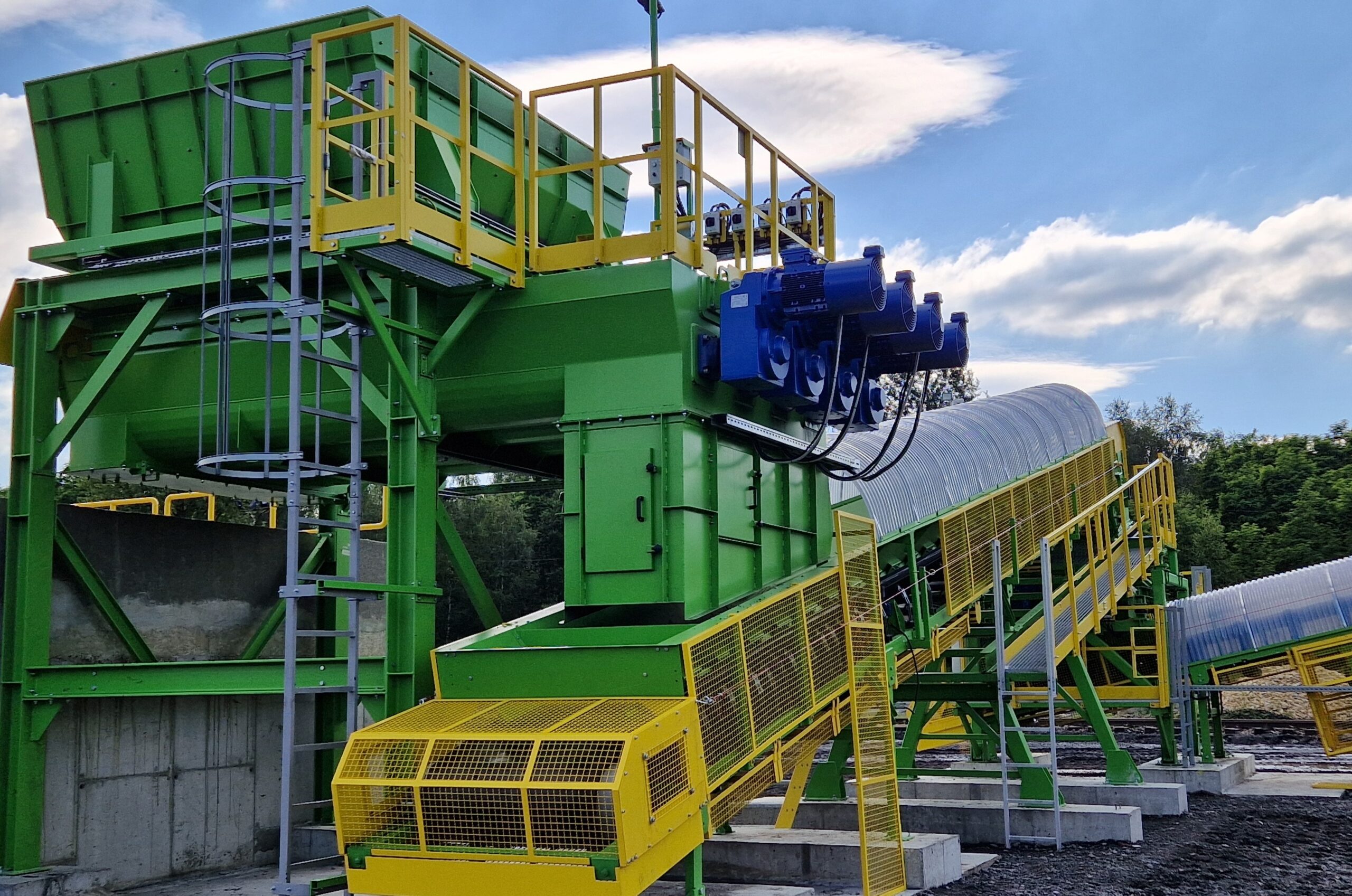
Linia granulacji miału węglowego
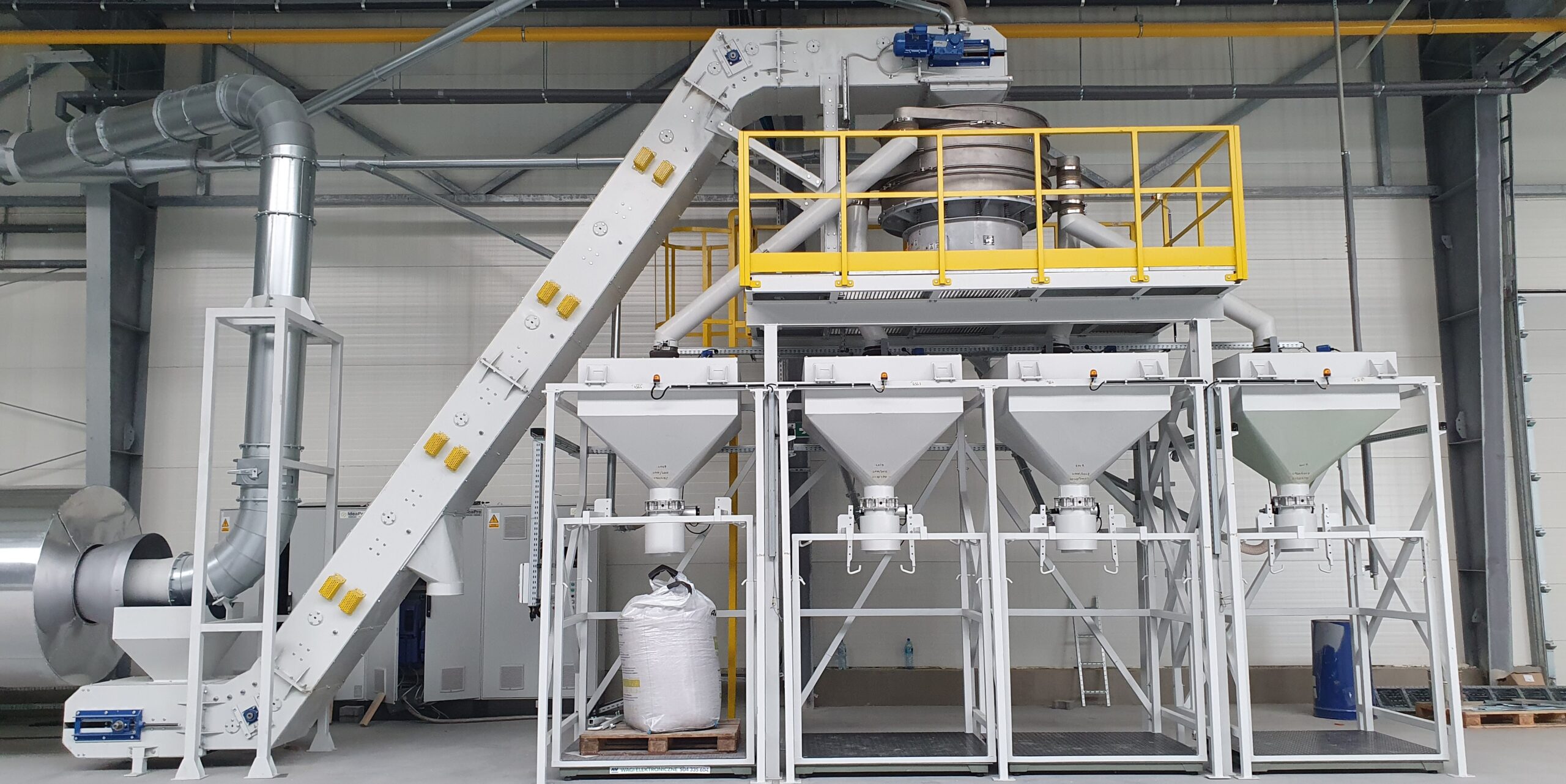
Linia granulacji, suszenia i przesiewania granulatów wapiennych
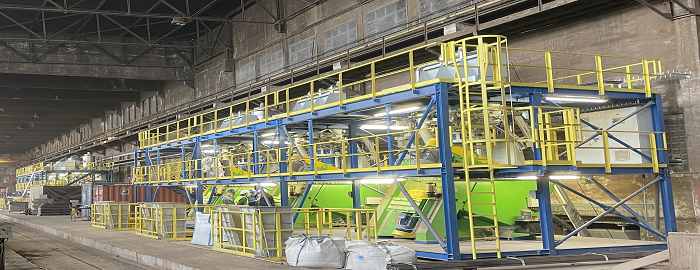
Linia granulacji proszków ceramicznych
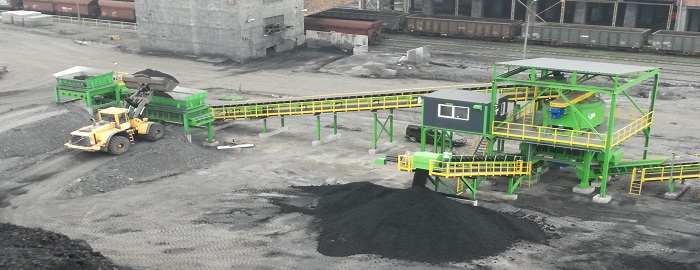
Linia granulacji miału węglowego z pyłem węglowym
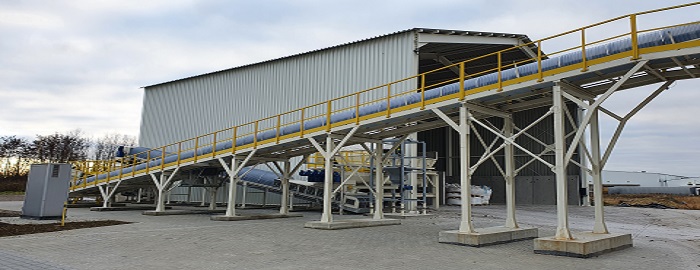
Załadunek materiałow do granulatora dymmamicznego MDV-26G
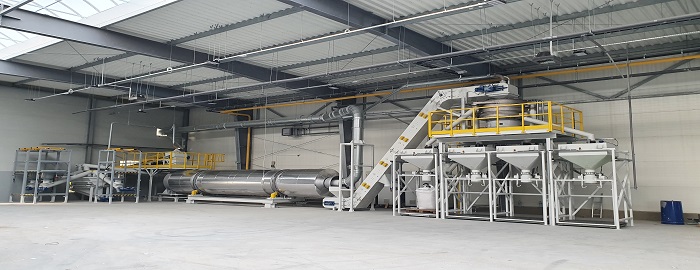
Linia granulacji materiałów sypkich i proszkowych
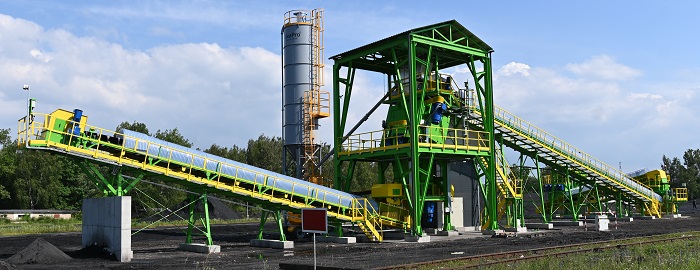
Linia granulacji mułu węglowego
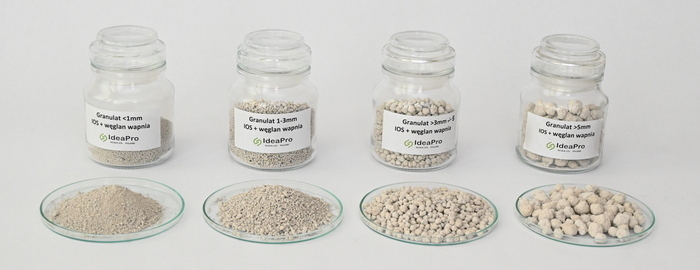
Granulat IOS + węglan wapnia
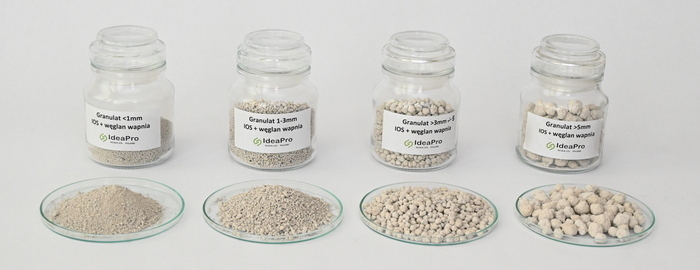
Granulat IOS + węglan wapnia
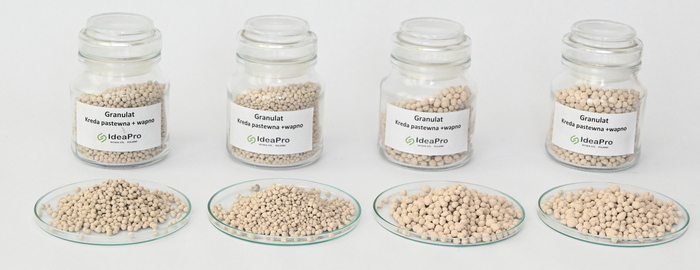
Granulat kredy pastewnej i wapna
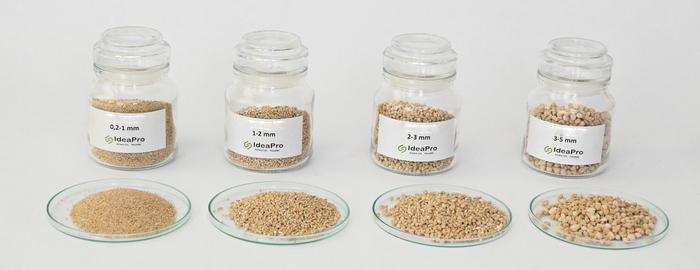
Granulat siarczanu magnezu
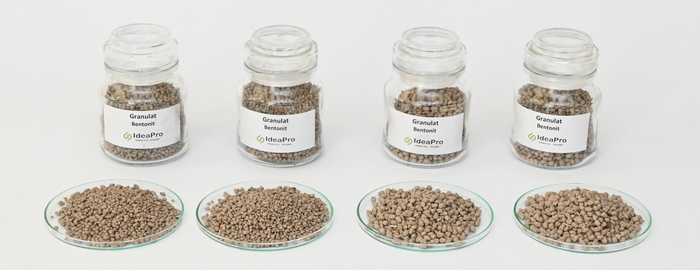
Granulat bentonitu
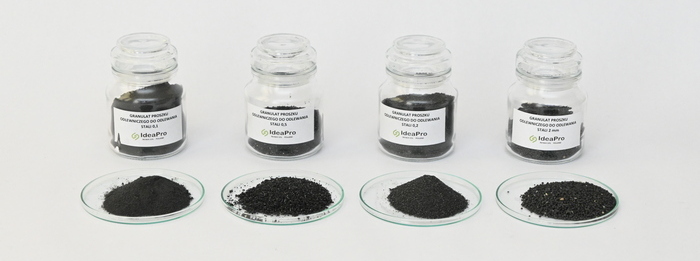
Mikrogranulat proszku odlewniczego do odlewania stali
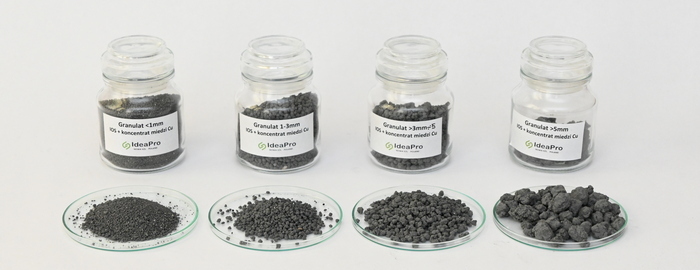
Granulat IOS i koncentratu miedzi
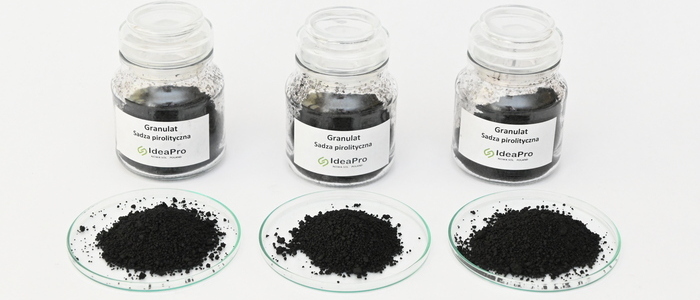
Granulat sadzy pirolitycznej
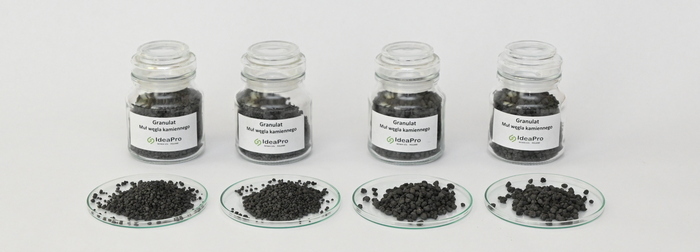
Granulat mułu węgla kamiennego
Specjaliści IdeaPro posiadający wieloletnie doświadczenie w projektowaniu, produkcji oraz eksploatacji urządzeń do granulacji służą pomocą w doborze odpowiedniego urządzenia zgodnej z wymaganiami klienta co do wielkości i wydajności.
W wielu przypadkach pomoc naszych specjalistów jest nieodzowna szczególnie w:
- w usytuowaniu urządzeń w istniejących obiektach lub planowanej lokalizacji
- wykonaniu założeń branżowych, jak: instalacje elektryczne, sprężonego powietrza, instalacji wodnej lub innych wymaganych projektów, np. do pozwolenia na budowę
- opracowaniu projektu fundamentów
- doborze system odpylania dostosowanego do warunków pracy granulatora
- optymalizacji procesu granulacji oraz wydajności
- w pozyskaniu środków z UE oraz innych programów
Wszelkie bardziej szczegółowe pytania prosimy kierować bezpośrednio do IdeaPro.
Nasz doświadczony zespół specjalistów chętnie udzieli Państwu wszelkich informacji i pomocy.