VACUUM - PROCES (V-proces) stosowany jest do wykonywania odlewów małych, dużych oraz cienkościennych z możliwością stosowania rdzeni. Znalazł zastosowanie głównie do produkcji małoseryjnej odlewów o dużych gabarytach.
W „V-proces” zagęszcza się i wiąże piasek odlewniczy różnicą ciśnienia pomiędzy ciśnieniem zewnętrznym (atmosferycznym), a wytworzonym podciśnieniem (próżnią) wewnątrz formy. W procesie formowania używany jest piasek suchy bez lepiszcza i wody. Forma skrzynkowa z obu stron pokryta jest cienką folią, która zasysana jest do powierzchni formy. Charakterystyczną cechą procesu jest zastosowanie do formowania suchego, drobnoziarnistego piasku odlewniczego bez środka wiążącego. Środkiem wiążącym jest podciśnienie w zakresie 30 ÷ 60 kPa (0,3 ÷ 0,6 bar) wytwarzane w przestrzeni zamkniętej.
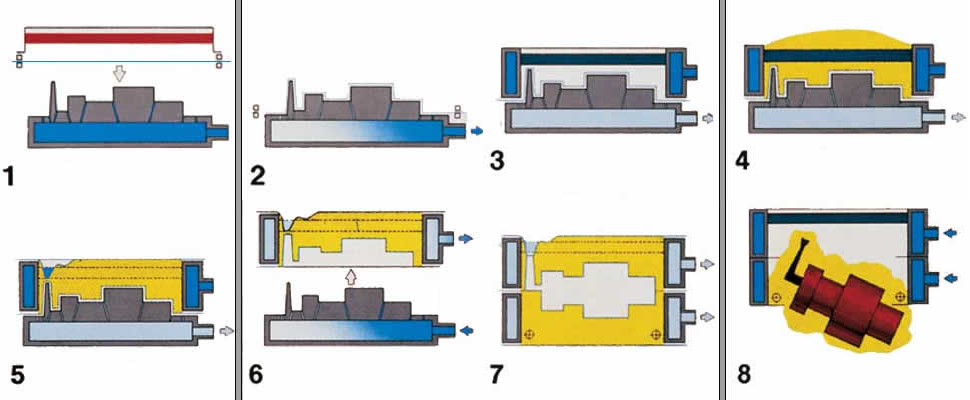
Etapy formowania „V-proces”
1- podgrzanie foli, 2– pokrycie folią płyty modelowej, odsysanie powietrza, 3- nałożenie skrzyni formierskiej na płytę modelową, 4- wypełnienie skrzyni suchym piaskiem oraz zagęszczenie wibracyjne - zwiększenie gęstości pozornej piasku, 5- nałożenie foli na górną powierzchnię formy, 6- odsysanie powietrza ze skrzyni formierskiej i jej zdjęcie z płyty modelowej oraz jednoczesne rozszczelnienie płyty modelowej, 7- złożenie formy, 8- usunięcie zawartości skrzynek
Wykonywanie form, ich transport, zalewanie oraz wybijanie może być realizowane na pojedynczych stanowiskach formierskich lub na liniach formierskich typu LFV. Linie Formierskie LFV, vacuum-proces, projektowane są oraz wykonywane jako układy modułowe o różnych wydajnościach oraz różnych wielkościach skrzyń formierskich, dostosowane do warunków lokalizacyjnych odlewni. Przeznaczone są do wykonywania odlewów o różnych kształtach, rozmiarach oraz z różnych stopów metali (brąz, mosiądz, aluminium, żeliwo oraz staliwo) w cyklu automatycznym lub półautomatycznym. Wykonywanie form i kolejne operacje technologiczne mogą być zautomatyzowane w takim samym stopniu, jak w liniach odlewniczych wykonujących formy w technologii mas formierskich bentonitowych lub samoutwardzalnych.
W „V-proces” obie połówki formy są wykonywane z użyciem specjalistycznej maszyny formierskiej. Na stole obrotowym maszyny formierskiej zamocowane są dwie płyty modelowe obu części formy. Pierwszym etapem formowania jest założenie podgrzanej folii na górną płytę modelową na pierwszym (przednim) stanowisku maszyny formierskiej. W czasie zakładania foli pod płytą modelową podłączone jest podciśnienie, a przez to następuje zassanie podgrzanej, elastycznej folii do płyty modelowej i modelu, powodując jej dokładne przyleganie. Następnie na płytę modelową, pokrytą folią, zakładana jest górna skrzynka.
W tym czasie na drugim (tylnym) stanowisku maszyny formierskiej do dolnej skrzynki z płytą modelową, pokrytą wcześniej folią, dozowana jest porcja suchego piasku.
Po wykonaniu opisanych powyżej czynności następuje obrót stołu maszyny formierskiej ze skrzynkami formierskimi. Na pierwszym stanowisku dolna skrzynka formierska wypełniona piaskiem zostaje podłączona do instalacji podciśnieniowej co powoduje zagęszczenie i utwardzenie piasku wewnątrz skrzynki. Powierzchnia górna skrzynki zostaje pokryta folią, która natychmiast zostaje zassana do powierzchni górnej skrzynki i piasku wskutek podciśnienia, wytworzonego wewnątrz skrzynki. Do skrzynki dolnej zostaje podłączony wąż transportowy instalacji podciśnieniowej; jednocześnie wytwarza się podciśnienie pod płytą modelową. Tak przygotowana półforma zostaje oddzielona od płyty modelowej i przetransportowana na stanowisko składania skrzynek.
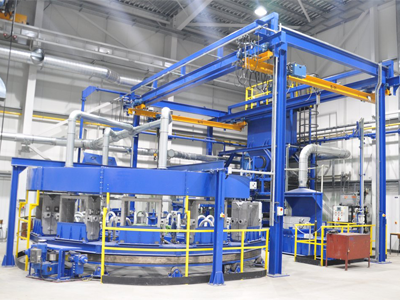
Linia formierska LFV ”V-PROCES”
Obrót stołu maszyny formierskiej, nakładanie foli oraz nasypywanie piasku do skrzynek formierskich jest realizowane w cyklu automatycznym. Wszystkie czynności związane z nakładaniem foli, na płyty modelowe oraz powierzchnie skrzynek formierskich, cięciem folii oraz jej podgrzewaniem wykonywane są w cyklu automatycznym przez zespół nakładania foli.
W ten sam sposób w maszynie formierskiej wykonywana jest półforma górna, która transportowana jest na stanowisko składania skrzyń. Na tym stanowisku po ewentualnym założeniu rdzeni w półformie dolnej następuje złożenie skrzyń oraz ich sklamrowanie. Składanie skrzyń wykonywane jest w pozycji poziomej. Gotowa forma zostaje umieszczona na specjalnym uchwycie transportowym i podłączona do kolejnego węża transportowego z podciśnieniem.
Tak przygotowana kompletna forma zostaje przetransportowana przez operatora za pomocą wciągnika elektrycznego na karuzelę (stół obrotowy) i umieszczona w pozycji pionowej na stanowisku zalewania form. Na tym stanowisku forma automatycznie zostaje podłączona do instalacji podciśnieniowej stołu obrotowego i operator odłącza wąż transportowy z podciśnieniem. Karuzela wykonuje skokowy obrót (o jedną podziałkę), w ten sposób forma przemieszcza się na stanowisko zalewania, na którym następuje zalanie form ciekłym metalem z kadzi odlewniczej lub pieca do zalewania.
Tworzywo folii w czasie procesu zalewania w wyniku działania podciśnienia w formie odparowuje i przenika do formy, tworząc wraz z zastosowanym pokryciem i z cząsteczkami piasku cienką warstwę powłoki.
Kolejny obrót karuzeli o jedną podziałkę przemieszcza zalane ciekłym metalem formy na stanowisko chłodzenia. W czasie zalewania i chłodzenia odlewu zestaw skrzynek formierskich jest podłączony do instalacji podciśnienia. Większość powstających gazów i spalin zasysana jest, co znacząco wpływa na obniżenie emisji do otoczenia.
Wystudzone formy ponownie podłączane są do węża transportowego z podciśnieniem i za pomocą specjalnego uchwytu transportowego zabierane są przez operatora na stanowisko wybijania odlewów z formy (skrzyń formierskich). Proces wybijania odlewu, a właściwie jego wyjmowanie ze skrzynki formierskiej polega na odłączeniu od instalacji podciśnieniowej i wysypaniu suchego piasku.
W „V-proces” wykonane formy przez cały czas muszą być podłączone do instalacji podciśnieniowej, dlatego też linie formierskie wykonywane są w większości jako półautomatyczne o małej i średniej wydajności.
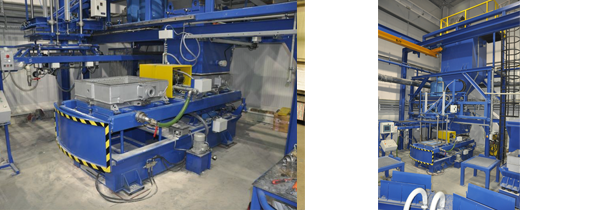
Maszyna formierska ”V-proces” (stanowisko wykonywania form)
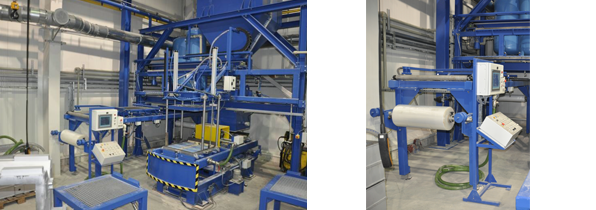
Stanowisko nanoszenia foli na płytę modelową i skrzynki formierskie
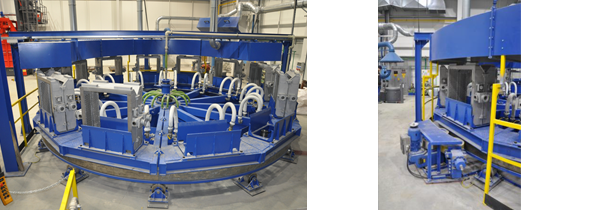
Karuzela (stół obrotowy) do zalewania skrzynek linii formierskiej
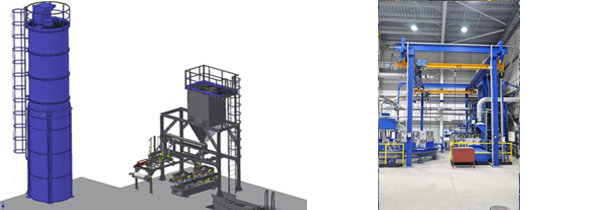
Stanowisko wyjmowania odlewów ze skrzynek formierskich
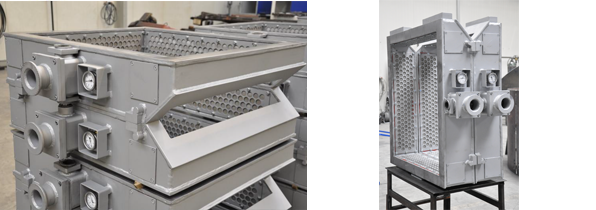
Skrzynki formierskie
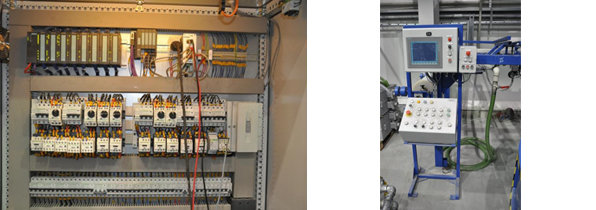
System sterowania elektronicznego linii formierskiej LFV
Zalety ”V - PROCES” V-Proces zyskał na znaczeniu ze względu na możliwość wykonywania odlewów o dużej dokładności wymiarowej, nawet z tolerancją ± 0,3mm, oraz bardzo dobrej jakości uzyskiwanej powierzchni odlewów. W niektórych przypadkach można zmniejszyć lub wyeliminować obróbkę mechaniczną odlewu.
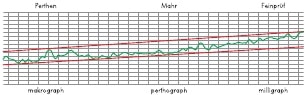
Odlewanie ”V- PROCES”
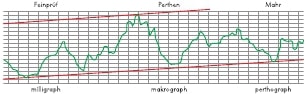
Odlewanie w masach samoutwardzalnych
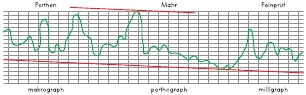
Odlewanie w masach na wilgotno
Chropowatość powierzchni odlewów dla różnych metod formowania
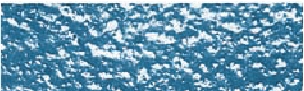
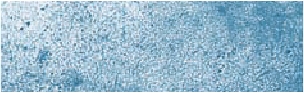
Jakość powierzchni aluminium po piaskowniu dla odlewania w stałych formach (powyżej) i odlewanie podciśnieniowe (poniżej)
Technologia formowania | Chropowatość powierzchni [Ra] | Minimalne pochylenie [°] | Minimalna grubość ścianek odlewu [mm] |
V - PROCES | 3,2 ÷ 6,4 | bez ograniczeń | 3,2 |
I generacja | 5 ÷ 14 | 1 do 5 | 6,3 |
Precyzyjny odlew (model woskowy) | 1,6 ÷ 3,2 | bez ograniczeń | 1,5 |
Forma grafitowa (stała, permanentna) | 3,8 ÷ 7,6 | 2 do 5 | 4,7 |
Formy gipsowe | 1,6 ÷ 3,2 | 0,5 do 2 | 1,8 |
Formy gipsowe | 0,8 ÷ 1,6 | 1 do 3 | 0,7 do 1,5 |
Charakterystyka porównawcza parametrów odlewów wykonanych metodą ”V- PROCES” |
- V-procesie nie wymagana pochylenia odlewniczego, co umożliwia wykonywanie odlewów o jednakowej grubości ścianek na całej wysokości. Umożliwia to zmniejszenie ciężaru odlewu oraz często eliminuje konieczność stosowania obróbki skrawaniem.
- Istotnym jest również brak niszczenia i zużywania modeli w procesie formowania, co pozwala na stosowanie „miękkich” materiałów, takich jak żywice lub drewno.
- Oprócz wysokiej dokładności wymiarowej i małej chropowatości powierzchni, stosowane w tym procesie modele są tanie w wykonaniu oraz są trwałe.
- Zaletą V-procesu jest mała szkodliwość dla środowiska, brak materiałów wiążących, łatwość odprowadzania gazów i spalin wytwarzanych w procesie zalewania form piaskowych oraz niski koszt jednostkowy produkcji odlewów.
- Proces ten może być realizowany przy wytwarzaniu odlewów o różnych wymiarach. W odlewniach rosyjskich z powodzeniem proces ten wykorzystuje się przy produkcji odlewów o dużych gabarytach.
- Omawiana technologia może zastąpić wytwarzanie dużych odlewów w formach z mas samoutwardzalnych, wymagających stosowania bardzo kosztownego procesu regeneracji.
Biorąc pod uwagę całkowite nakłady inwestycyjne na stworzenie nowego stanowiska formierskiego wraz z przygotowaniem masy formierskiej oraz regeneracją, okazuje się, że realizacja procesu V wymaga najmniejszych nakładów inwestycyjnych.
Realizacja procesu podciśnieniowego nie wymaga stosowania skomplikowanych maszyn formierskich, regeneracji, spoiwa oraz wody.
Linie formierskie LFV wyposażane są w elektroniczne systemy sterowania bazujące na sterownikach PLC, umożliwiające:
- automatyzację pracy,
- wizualizację i kontrolę procesu,
- rejestrację parametrów technologicznych,
- analizę stanów pracy poszczególnych urządzeń i mechanizmów z natychmiastową lokalizacją ewentualnych przyczyn awarii,
- serwis oraz nadzór nad pracą urządzeń online przez połączenie internetowe.
Linie formierskie LFV są projektowane i wykonywane dla różnych wymiarów skrzynek formierskich w „świetle” oraz dla różnych wydajności. Typowe gabaryty skrzynek formierskich produkowanych przez IdeaPro linii formierskich to:
wymiary skrzynek formierskich mogą odbiegać od typowych. Zmiana wymiarów oraz dobór wysokości skrzynek wymaga uzgodnienia ze specjalistami IdeaPro. Specjaliści IdeaPro, posiadający wieloletnie doświadczenie w projektowaniu, produkcji oraz eksploatacji linii formierskich, służą pomocą w doborze odpowiedniej linii formierskiej zgodnej z wymaganiami klienta co do wielkości skrzynek formierskich i wydajności.
W wielu przypadkach pomoc naszych specjalistów jest nieodzowna szczególnie w:
- pomocy w usytuowaniu, lokalizacji linii formierskiej w istniejących obiektach lub planowanej lokalizacji,
- wykonaniu założeń branżowych, jak: instalacje elektryczne, sprężonego powietrza, instalacji wodnej lub innych wymaganych projektów, np. do pozwolenia na budowę,
- wykonanie założeń fundamentowych lub projektu fundamentów,
- doborze odpowiedniego system odpylania dostosowanego do warunków pracy linii,
- pomocy w pozyskaniu środków z UE oraz innych programów.
Nasz doświadczony zespół specjalistów chętnie udzieli Państwu wszelkich informacji i pomocy.