W odlewniach wytwarzanie odlewów odbywa się w formach piaskowych wykonywanych przede wszystkim z masy syntetycznej z bentonitem, odświeżanej w kolejnych obiegach. Technologia ta jest w dalszym ciągu rozwijana ze względu na możliwość stosowania coraz to doskonalszych rozwiązań mechanizacji i automatyzacji.
Stanowisko formierskie doświadczalne typ FTD-65 dedykowane jest dla uczelni oraz instytutów naukowych, zajmujących się technologiami formowania w masach formierskich z bentonitem.
Stanowisko wykonane zostało dla Półtechniki Łódzkiej „Katedra Technologii Materiałowych i Systemów Produkcji”, dla potrzeb dydaktycznych uczelni. Stanowisko umożliwia wykonywanie form górnych oraz dolnych w różnych znanych i stosowanych na świecie technologiach zagęszczania form:
- Technologia zagęszczania form impulsowa, strumieniowa z prasowaniem.
- Technologia zagęszczania form impulsem sprężonego powietrza (proces IdeaPro).
- Technologia zagęszczania form strumieniem sprężonego powietrza (proces „Seiatsu”).
- Technologia zagęszczania form metodą wstrzeliwania masy formierskiej z prasowaniem.
- Technologia zagęszczania form metodą prasowania.
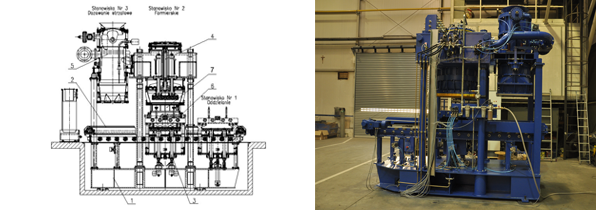
Stanowisko formierskie doświadczalne FTD-65
1-konstrukcja nośna, 2-zespół przejazdu stołu, 3-zespół podpierania prasy i oddzielania, 4-zespół impulsowy z prasą, 5-zespół strzałowy, 6-nośnik płyt modelowych, 7-ramka nadmiarowa, 8-instalacja hydrauliczna, 9-instalacja pneumatyczna
Charakterystyka techniczna stanowiska formierskiego doświadczalnego FTD-65
Wymiary skrzynki formierskiej w świetle | Długość | mm | 630 |
Szerokość | mm | 500 | |
Wysokość | mm | 200 | |
Wymiary ramki nadmiarowej w świetle | długość | mm | 590 |
szerokość | mm | 490 | |
Wysokość ramki nadmiarowej dla skrzynki formierskiej o wysokości 200 dla technologii zagęszczania impulsowego oraz strumieniowego | mm | 160 | |
Wysokość ramki nadmiarowej dla skrzynki formierskiej o wysokości 200 dla technologii zagęszczania przez wstrzeliwanie | mm | 60 | |
Głębokość modelu ujemnego (max) | mm | 140 | |
Ciśnienie sprężonego powietrza do impulsu | MPa | 0,2÷0,6 | |
Maksymalny. skok zespołu oddzielania | mm | 255 | |
Maksymalna odległość ramki nadmiarowej od skrzynki formierskiej po oddzieleniu | mm | 45 | |
Ciśnienie sprężonego powietrza | MPa | 0,6÷0,7 | |
Napięcie zasilania | V | 3x400V/50Hz | |
Napięcie sterowania | V | 24 | |
Moc zainstalowana | kW | 8,6 | |
Minimalna temperatura pracy maszyny | °C | +5 |
1. Technologia zagęszczania form impulsowa, strumieniowa z prasowaniem.
Stanowisko formierskie doświadczalne FTD-65 umożliwia zagęszczanie form technologią impulsową oraz technologią strumieniową (proces „Seiatsu”), które polegają na wstępnym zagęszczeniu masy formierskiej impulsem lub strumieniem sprężonego powietrza oraz dogęszczeniu przez prasowanie za pomocą hydraulicznego zespołu prasującego, głowicą sztywną, przeponową lub głowicą wielotłoczkową.
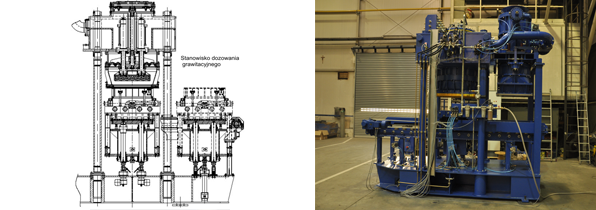
Stanowisko zagęszczania form technologią impulsową, strumieniową (proces „Seiatsu”) oraz prasowaniem
Proces zagęszczania impulsowego i strumieniowego z prasowaniem polega na:
- wstępnym zagęszczeniu masy formierskiej poprzez jej dozowanie grawitacyjne lub dozowanie za pomocą narzucarko-spulchniarki do zestawu formierskiego: nośnik płyty modelowej, płyta modelowa, skrzynka formierska oraz nadstawka,
- zagęszczeniu I stopnia za pomocą niskociśnieniowego impulsu (proces „IdeaPro”) lub strumienia sprężonego powietrza (proces „Seiatsu”),
- zagęszczeniu II stopnia (ostateczne) dla technologii impulsowej za pomocą prasowania pod średnimi naciskami (p0,6MPa), dla technologii strumieniowej za pomocą prasowania pod wysokimi naciskami (p≥0,6MPa).
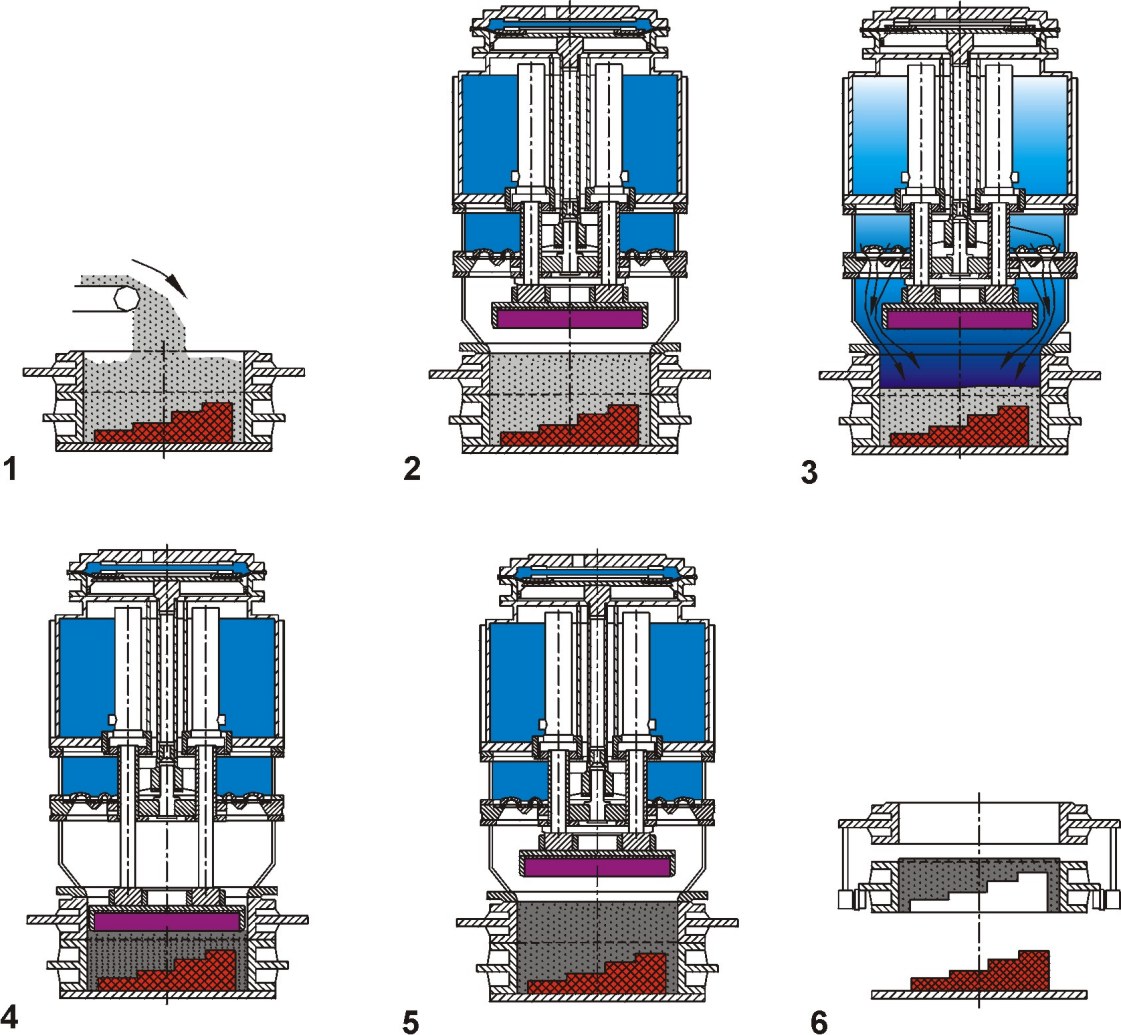
Fazy procesu zagęszczania form technologią impulsową oraz strumieniową z prasowaniem: 1- dozowanie masy formierskiej, 2- zwieranie zestawu formowego:
płyta modelowa, skrzynka formierska, ramka nadmiarowa z głowicą strzałową, 3- zagęszczanie impulsowe lub strumieniowe sprężonym powietrzem, 4- prasowanie, 5- rozwieranie układu, 6- oddzielanie modelu od formy
2. Technologia zagęszczania form impulsem sprężonego powietrza (proces IdeaPro). Proces zagęszczania impulsowego stosowany jest przez IdeaPro Nowa Sól - Polska, Foundry Automation - Italia, Künkel Wagner – Niemcy, realizowana jest przy gradiencie ciśnienia powyżej 10 MPa/s i dochodzi do 300 MPa/s. Tak szybki przyrost ciśnienia powoduje, że impuls sprężonego powietrza ma wystarczającą dynamikę, aby w bardzo krótkim czasie zagęścić masę formierską. Dlatego zawory impulsowe maszyn formierskich cechują się nagłym otwarciem i natychmiastowym jego zamknięciem. W efekcie ilość sprężonego powietrza niezbędna do prawidłowego zagęszczenia formy jest bardzo mała, pozwala to na zastosowanie małego zbiornika sprężonego powietrza zabudowanego wewnątrz maszyny formierskiej.
Formowanie impulsowe nie wymaga tak dużej powierzchni odpowietrzającej. W praktyce, dla modeli średnio-skomplikowanych, odpowietrzanie formy sprowadza się do zamontowania odpowietrzników w „martwym” polu formy, w pobliżu wewnętrznych ścianek skrzyni formierskiej. Stanowi to przeważnie powierzchnię ok. 1% powierzchni formy i maleje wraz ze wzrostem wielkości skrzyni formierskiej.
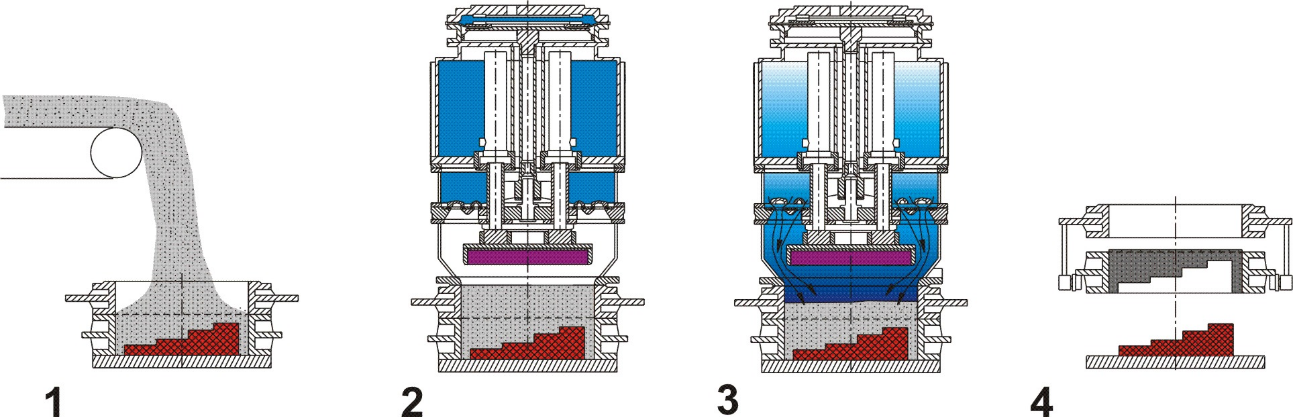
Fazy procesu zagęszczania form technologią impulsową oraz strumieniową: 1- dozowanie masy formierskiej, 2- zwieranie zestawu formowego: płyta modelowa, skrzynka formierska, ramka nadmiarowa z głowicą strzałową, 3- zagęszczanie impulsowe lub strumieniowe sprężonym powietrzem, 4- oddzielanie modelu od formy
3. Technologia zagęszczania form strumieniem sprężonego powietrza (proces „Seiatsu”). Proces SEIATSU firmy Heinrich Wagner Sinto – Niemcy, polega na wstępnym zagęszczeniu masy formierskiej strumieniem sprężonego powietrza oraz dogęszczeniu zasadniczym za pomocą hydraulicznego zespołu prasującego, najczęściej z udziałem głowicy sztywnej, przeponowej lub głowicy wielotłoczkowej.
Proces formowania strumieniowego realizowany jest przy szybkości narastania ciśnienia do ok. 1MPa/s. Przy formowaniu strumieniowym zawór impulsowy otwarty jest przez około 1,2s, przepuszczając do formy dużą ilość sprężonego powietrza. Strumień powietrza, przeciskając się przez masę formierską po najmniejszych liniach oporu, działa na nią zagęszczająco. Po dojściu w obszar płyty modelowej uchodzi do atmosfery przez odpowietrzniki.
Dla skutecznej realizacji formowania strumieniowego należy stosować znaczne odpowietrzenie płyty modelowej, aby odprowadzić do atmosfery zużyte powietrze. W praktyce, przy formowaniu strumieniowym z udziałem skomplikowanych modeli, stosuje się odpowietrzanie płyty modelowej dochodzące do 8% powierzchni skrzyni formierskiej. Wówczas znaczna powierzchnia odpowietrzania odbywa się kosztem powierzchni przewidzianej na model. Ze względu na dużą ilość zużywanego sprężonego powietrza w procesie strumieniowym wymagany jest obok maszyny, dodatkowy zbiornik sprężonego powietrza. Formowanie strumieniowe (np. proces SEIATSU) wymaga dodatkowego dogęszczania formy w zakresie średnich i wysokich nacisków jednostkowych; tzw. „przeprasowanie” odbywa się na całej wysokości formy. Wymaga to dodatkowo wykonywania w formie otworów odpowietrzających dla odgazowywania jej w czasie procesu zalewania ciekłym metalem. Prasowanie na całej wysokości formy wiąże się również bezpośrednio ze zwiększoną energochłonnością maszyny oraz trudniejszym procesem wypychania formy ze skrzynki formierskiej.
4. Technologia zagęszczania formy metodą wstrzeliwania masy formierskiej z prasowaniem.
Technologia zagęszczenia (proces FBO firmy Heinrich Wagner Sinto - Niemcy, DISAMATIC oraz DISA MATCH firmy DISA – Dania), polega na:
- zagęszczeniu I stopnia za pomocą wstrzelenia masy formierskiej z komory strzałowej do zestawu formierskiego: nośnik płyty modelowej, płyta modelowa, skrzynka formierska oraz nadstawka. Zagęszczanie I stopnia nie może występować samoistnie, może być realizowane tylko dla celów porównawczych z innymi technologiami zagęszczania oraz dla celów dydaktycznych.
- zagęszczeniu II stopnia (ostateczne) za pomocą prasowania pod wysokimi naciskami (p≥0,6MPa).
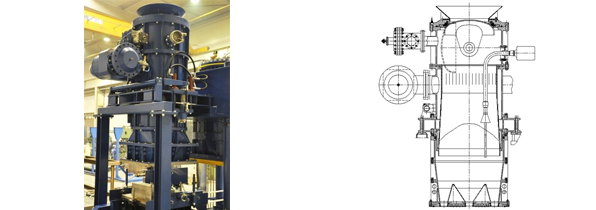
Stanowisko zagęszczana form technologią wstrzeliwania masy formierskiej z prasowaniem
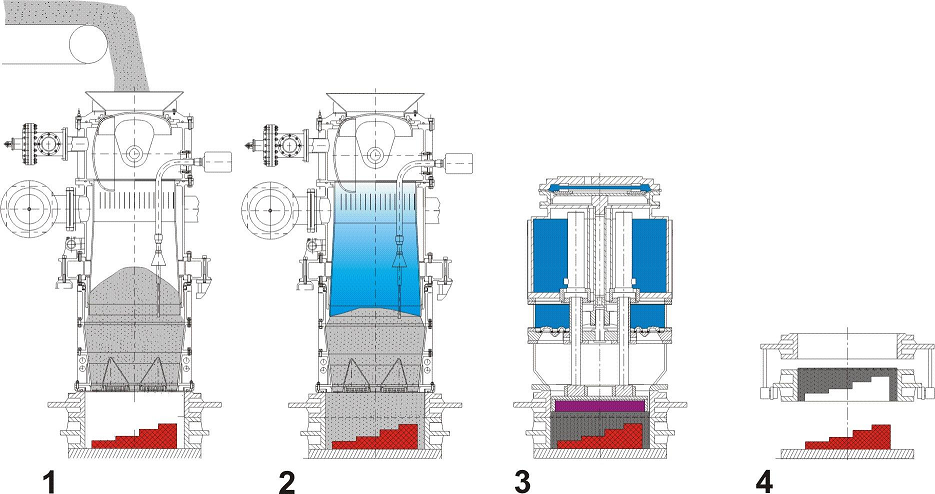
Fazy procesu zagęszczania form technologią wstrzeliwania masy z prasowaniem:
1- dozowanie masy formierskiej, 2- zwieranie zestawu formowego: płyta modelowa, skrzynka formierska, ramka nadmiarowa z głowicą strzałową, 3- prasowanie, 4- oddzielanie modelu od formy
W pierwszym etapie następuje wstępne zagęszczanie form masą formierską, które realizowane jest przez wstrzelenie masy formierskiej i następnie prasowanie na stanowisku formierskim.
W pierwszym etapie następuje zadozowanie masy formierskiej do zestawu skrzynia formierska – ramka nadmiarowa. Następuje przejazd korpusu jezdnego na stanowisko nr2. Podczas przejazdu górne powierzchnie ramki nadmiarowej czyszczone są szczotkami zainstalowanymi na głowicy impulsowo – prasującej.
Na stanowisku nr 2 cały zestaw formierski jest podnoszony czterema cylindrami hydraulicznymi do zwarcia z głowicą impulsowo – prasującą w celu uszczelnienia komory roboczej powstałej pomiędzy zestawem formierskim a zaworem impulsowym.
Na stanowisku nr 2 następuje doprasowanie stemplem prasującym znajdującym się wewnątrz komory roboczej głowicy impulsowo –
prasującej. Po prasowaniu zestaw formierski przemieszcza się na stanowisko nr 1 w celu wykonania operacji oddzielania. Po powrocie na stanowisko oddzielania listwy rolkowe. zespołu oddzielania wykonują ruch ku górze podnosząc najpierw ramkę nadmiarową na ok. 45 mm. Potem rozpoczyna się podnoszenie skrzynki formierskiej znad płyty modelowej i w efekcie oddzielenie półformy od modelu.
Prędkość ruchu oddzielania jest regulowana i może być nastawiona w funkcji drogi podnoszenia (opuszczania).
Po osiągnięciu górnego poziomu zespołu oddzielania zaformowana skrzynia jest gotowa do przemieszczania poza formierkę.
Po odmuchaniu i odpowiednim przygotowaniu zespołu modelowego na stanowisko nr 1 można wprowadzić następną pustą skrzynkę i cykl powtórzyć.
5. Technologia zagęszczania form metodą prasowania.
Zagęszczanie form technologią prasowania jest najstarszą i jedną z bardziej znanych technik formowania. Polega na zagęszczeniu masy formierskiej za pomocą hydraulicznego zespołu prasującego, proces ma na celu zmniejszanie wolnych przestrzeni między ziarnami piasku w otoczeniu z bentonitem i pyłem węglowym, co w efekcie powoduje dociśnięcie (odwzorowanie) masy formierskiej do modelu, do ścian skrzyni formierskiej i do płyty modelowej. Prasowanie daje możliwość uzyskania wysokiego stopnia zagęszczenia wcześniej zagęszczonej masy, formy mają wysoką wytrzymałość mechaniczną, dokładność wymiarów i ostrość krawędzi. Powstaje forma odlewnicza, w której odwzorowane od modelu powierzchnie są w stanie oprzeć się sile naporu zalewanego ciekłego metalu, a jednocześnie odprowadzi ona gazy powstające przy zalewaniu i stygnięciu metalu.
Proces prasowania w różnych maszynach jest realizowany w różnych wariantach, zależnie od konstrukcji zespołów prasujących, kinematyki współpracujących elementów lub mediów roboczych. Wspólną cechą wszystkich rozwiązań jest stosunkowo wolne przemieszczanie się cząstek masy zarówno względem siebie, jak i względem stałych punktów odniesienia (ścianek modelu, skrzynek itp.) podczas procesu zagęszczania.
Technologia zagęszczania przez prasowanie może być stosowana do niskich skrzyń formierskich (zalecana wysokość formy do 150 mm) oraz stosunkowo prostych (płaskich) odlewów.
Stanowisko doświadczalne FTD-65 wyposażone jest w sterownik swobodnie programowalny PLC, który umożliwia realizacje różnych funkcji, jak: nastawę parametrów technologicznych, wizualizację procesu formowania oraz archiwizację danych. Wykonywanie form realizowane jest w cyklu automatycznym.
Oferujemy pomoc naszych specjalistów szczególnie w:
- usytuowaniu, lokalizacji maszyny formierskiej w istniejących obiektach,
- wykonanie założeń fundamentowych lub projektu fundamentów,
- doborze odpowiedniego systemu dozowania masy formierskiej,
- optymalizacji przebiegu procesu technologicznego w zakresie doboru parametrów,
- pomocy w pozyskaniu środków z UE oraz innych programów.
Nasz doświadczony zespół specjalistów chętnie udzieli Państwu wszelkich informacji i pomocy.